Stainless steel: six common questions
Stainless steel is used in everything from aircraft and bridges to the kitchen sink, and you’ll find it almost everywhere!
Here, we look into this versatile material with our in-depth guide to stainless steel.
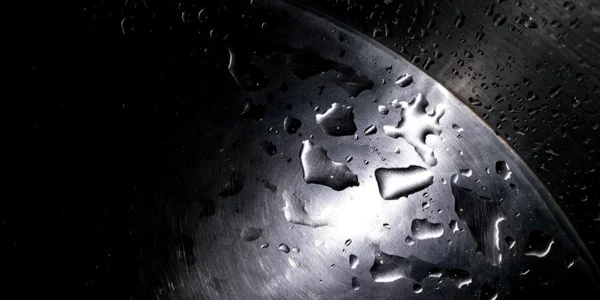
What is stainless steel?
Stainless steel is the general term for a group of corrosion-resistant alloy steels, which contain ≥ 10.5% chromium.
As an endlessly recyclable material, stainless steel leaves a minimal carbon footprint and has an extremely high recovery rate in the construction sector because of its longevity.
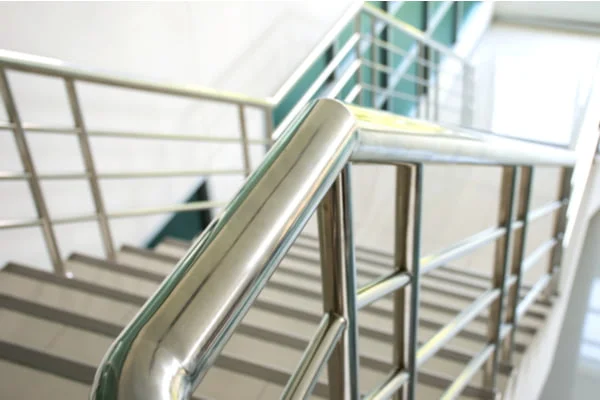
How does it work?
While both carbon steel and stainless steel contain iron – which oxidises when exposed to the environment – the added chromium in stainless steel makes it more corrosion resistant.
The chromium in stainless steel attaches itself to oxygen more readily than iron, creating a thin, stable film known as a chromium oxide layer.
This film protects the material by acting as a barrier that limits the amount of oxygen and water that can pass through to the underlying metal surface. If it is damaged, either mechanically or chemically, the film is self-healing.
Common steel does not have as much chromium content, which means it reacts with oxygen and allows it to bond with the iron, resulting in iron oxide (rust).
However, while stainless steel has more corrosion resistance than common steel, it is not immune to it. Extended exposure to environments of high humidity or high salinity, or exposure to certain fluids or chemicals can remove the protective layer of chromium oxide and lead to corrosion.
What are the different types of stainless steel?
While there are more than 60 grades of stainless steel, all are divided into five main types, typically based on their nickel content. Each group has different characteristics, and there are several grades within each group.
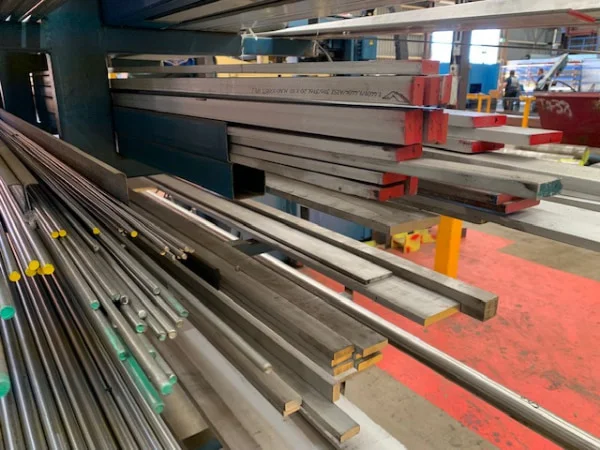
Austenitic
Austenitic steel is the most common type of stainless steel and is extremely high in nickel content. It generally contains large amounts of chromium, nitrogen and molybdenum.
Austenitic steel is a popular option because of its formability, fabricability and ductility. It has excellent corrosion resistance and cleanability, with good hygiene characteristics. It is non-magnetic (if annealed) and is hardenable by cold work only.
Grade 316 is a superior grade common type of austenitic stainless steel and is in stock at Edcon Steel. Known as the marine alloy, 316 has better corrosion resistance than other types of austenitic steels (particularly in marine environments) and can retain its toughness over the broadest temperature range.
304 grade is a widely used austenitic stainless steel variety, thanks to its resistance to corrosion and excellent workability, weldability and impact strength. Edcon Steel can source 304 stainless steel upon request.
Ferritic
Ferritic stainless steel contains no nickel and has low amounts of carbon. It is commonly used for products that will come into contact with corrosive materials – car components, cookware, industrial components – because of its resistance to stress corrosion cracking.
It has moderate to good corrosion resistance, but poor weldability. It is not hardenable by heat treatment. Common grades of ferritic stainless steel include 430 and 434.
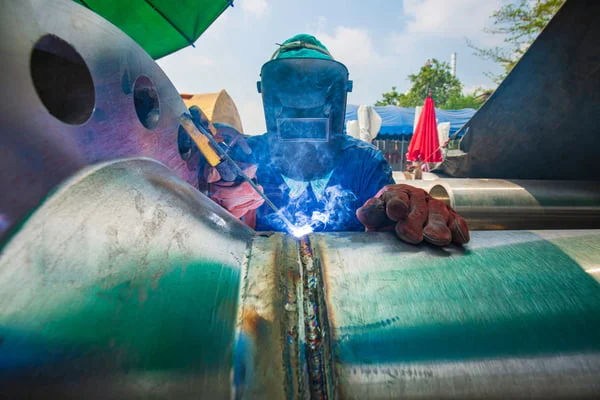
Duplex
While duplex stainless steel contains relatively high amounts of chromium, it only has moderate amounts of nickel. As such, it results in a combination of ferritic and austenitic structures, known as duplex.
Known for high resistance to stress corrosion cracking, duplex stainless steel has good weldability and formability and higher tensile and yield strength than either austenitic or ferritic steels.
Martensitic
Martensitic stainless steel has a relatively high carbon content and moderate corrosion resistance. While it can be hardened by heat treatment, which allows for high strength and hardness levels, martensitic steel has poor weldability.
What are the differences between 304 and 316 stainless?
The major difference between 304 and 316 stainless steel is the chemical composition, with grade 316 the only of the two containing molybdenum, which increases corrosion resistance.
However, the molybdenum content in grade 316 stainless steel can have adverse effects on formability and machinability, and then there are also cost impacts, as grade 316 stainless steel is generally more expensive than grade 304.
The most important factor to consider is if you have an application with very powerful corrosives or one that relies on chlorides, then paying a premium for grade 316 stainless steel will result in a product that will last many times longer than grade 304 stainless.
However, for applications using milder acids or where salt exposure isn’t a concern, grade 304 stainless steel can work just as well.
Learn more about the differences between grade 304 and grade 316 stainless.
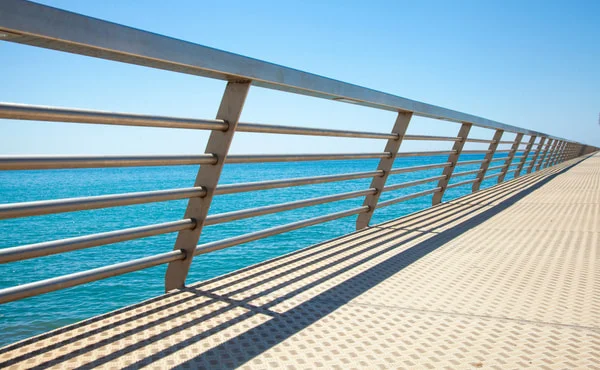
What are the benefits of stainless steel?
While famous for its corrosion resistance, stainless steel has a range of other benefits that are often overlooked.
Firstly, stainless steel has excellent high and low-temperature resistance.
High chromium and nickel-alloyed grades can resist scaling and retain strength at high temperatures, while other grades show extraordinary toughness in subzero temperatures.
The ease of fabrication for most stainless steels, as well as their strength-to-weight ratio, are other advantages.
The cold work hardening properties of certain grades can be used to decrease thickness and weight while strengthening the material, creating substantial reductions in costs.
Stainless steel is also aesthetically pleasing and available in a variety of surface finishes. Because it is easily cleaned and maintained, it is often the first choice for hospitals and food production facilities.
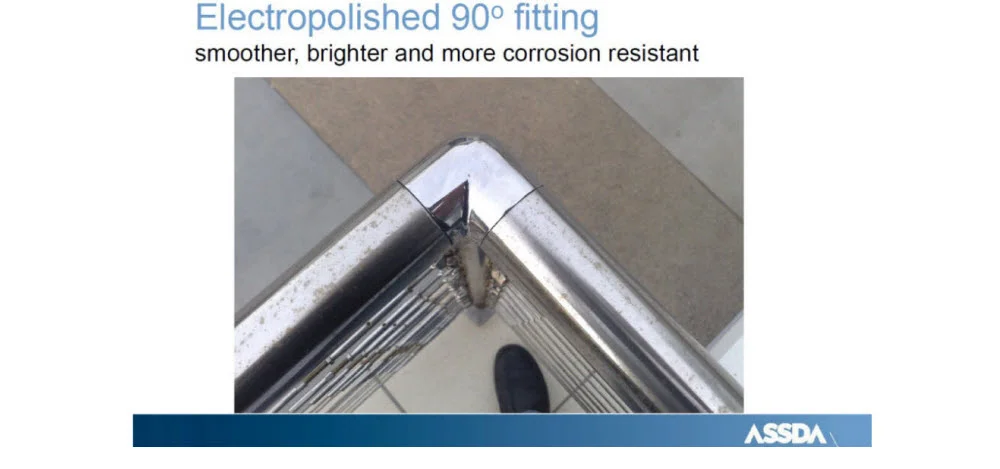
Why does stainless steel stain?
Many customers become frustrated when brown stains or rust appears on their ‘stainless’ steel, and rightly so. Without a lengthy chemistry lesson, these tea-coloured stains are due to the finish (surface roughness) and cleanliness of your stainless steel.
As a rule, the smoother the finish on your stainless steel, the less likely there will be small craters and crevices for contaminants to react (i.e. rust) to your stainless steel.
To protect your stainless steel, and for the best resistance to staining and discolouration, you should consider chemical cleaning (called passivation) as high or near to mirror polish as you can afford, along with a final electropolish.
A final word on staining with stainless steel is this – although unsightly for the customer in some situations, staining is a natural part of the protection of stainless steel. Unlike mild steel, the oxides (rust) on the surface of stainless steel protect the material below and stop corrosion from travelling further and causing more damage.
Your one-stop steel shop
Whether you want to know more about steel recycling or you’re looking for steel and metal products for your next project, we can help.
Edcon Steel is Australia’s most comprehensive online steel and metal superstore, so if you’re looking for products for your next project, we’ve got you covered. We cut and supply steel and metal – in a wide range of shapes, sizes and grades – for all your project needs.
Read more steel articles to find out more about the steel industry, customer projects and product resources.
Buy steel online. Delivery or in-store pick up.

Huge Stock
Levels

Buy Online
24/7

Custom Cut
or Order
