Heat treating processes for metals
Metal is one of the most versatile materials. Thanks to its mechanical and chemical stability, metal can be processed in many different ways… the possibilities are endless!
One of the most common methods of processing metals is heat treatment.
But heat treating metals can cover a range of techniques, each with the specific goal of improving your metal’s overall properties.
We take a look at what heat treating metal is and the various heat treatment techniques you can apply to your metal.
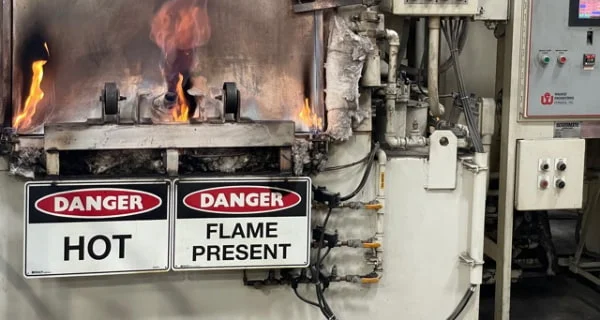
What is heat treating?
Heat treating refers to a set of metalworking techniques designed to alter the physical and chemical properties of metals.
These properties may include a metal’s hardness, ductility, malleability, toughness, grain structure and resistance to wear and tear.
Heat treating metal is an important industrial process that is done for a vast majority of all metal products used in various applications.
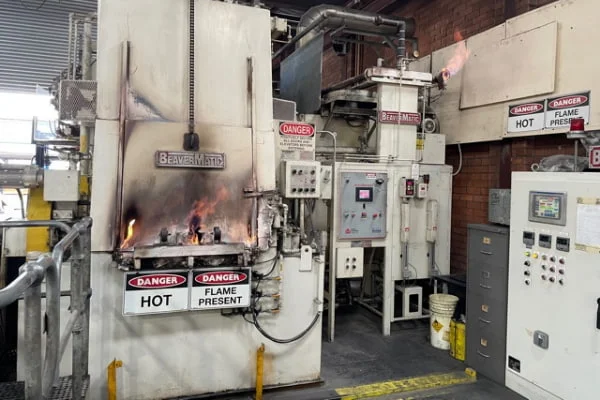
Choosing the right metals and heat treatment
Choosing your heat treatment for metal shouldn’t be an afterthought. It’s vital that customers understand each heat treatment’s process and the specifications you need for your metal.
As heat treating metal can change your metal’s dimensions, it’s hard to go back once a specific heat treatment is applied.
At Edcon Steel, we have partnerships with some of Sydney’s most reliable heat treatment services, including RJ Heat Treatment.
Wayne Post is a second-generation family owner of RJ Heat Treatment and our valued customers regularly utilise his heat treatment expertise.
Wayne believes that understanding the application of the metal before choosing your heat treatment is vital for any project.
“It’s really important that customers do their research. Customers need to consider what the specific job or application is, as different heat treatments can deliver various results. We encourage our customers to research what sort of materials they need, before jumping the gun and potentially choosing the wrong heat treatment,” says Wayne.
For example, ferrous metals account for the majority of heat treated materials, such as alloys of copper, magnesium, aluminum, nickel, brass and titanium. Ferrous metals that can be heat treated include cast iron, stainless steel and various grades of tool steel.
Copper and copper alloys are also subjected to heat treatment methods such as annealing, ageing and quenching. Another material suitable for heat treatment methods is aluminum. Heat treatment methods can include annealing, solution heat treating, natural and artificial ageing.
However, not all materials are suitable for the forms of heat treatment. Similarly, a single material will not necessarily benefit from each method, so every material must be studied separately to achieve the optimal results.
Understanding heat treatment methods doesn’t need to be difficult. We take a look at some of the most common heat treating techniques and how they can provide unique results for your metal.
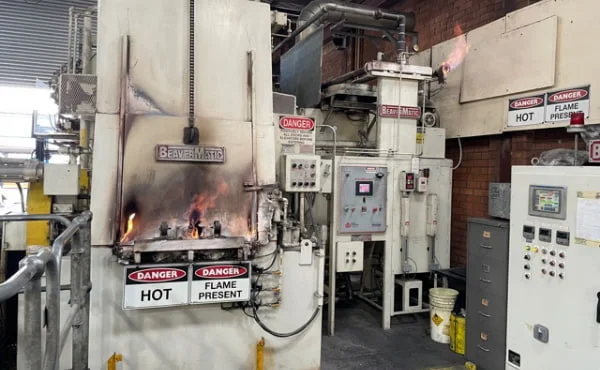
Annealing
Annealing is a process where the metal is heated to a specific temperature, then cooled very slowly.
This results in changes in the metal’s microstructure, often influencing its ductility, machinability and electrical conductivity.
Steel is the most common material to which annealing is done, but it’s also possible to anneal non-ferrous metals like copper and brass.
Depending on the temperature reached during heating, annealing can be classified into two sub-categories: normalising and stress relieving.
Normalising occurs when a metal is heated beyond its upper critical temperature. At this point, the recrystallisation of the particles in the metal becomes possible, resulting in a more ordered microstructure.
This eliminates the hardness that the metal may have as a result of cold working.
A less impactful method of annealing is stress relieving. The metal is heated to just below its critical temperature and cooled slowly. While this process does not change the hardness of the metal as much as normalising does, it is enough to release the internal stresses of the metal which may have come from cold working. The result is a sturdier and hard metal that is suitable for pressure vessels.
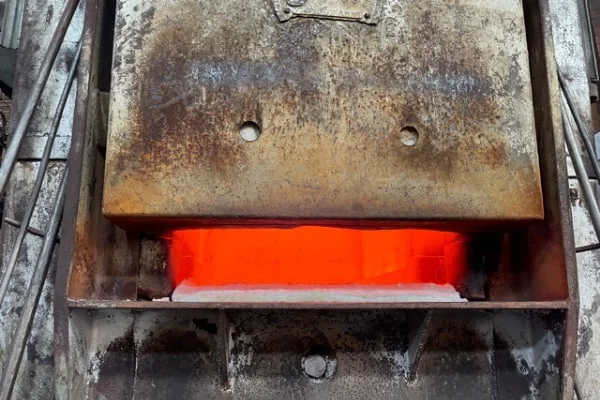
Case hardening
Case hardening is an ideal heat treatment for metals that require a wear-resistant surface and a tough core, such as gears, cams and cylinder sleeves.
The most common case-hardening processes are carburising and nitriding.
During the case-hardening process, low-carbon steel (either straight carbon steel or low-carbon alloy steel) is heated to a specific temperature in the presence of a material (solid, liquid or gas) that decomposes and deposits more carbon into the surface of a steel.
Once the part is cooled rapidly, the outer surface or case becomes hardened leaving the inside of the metal with a soft, but very tough core.
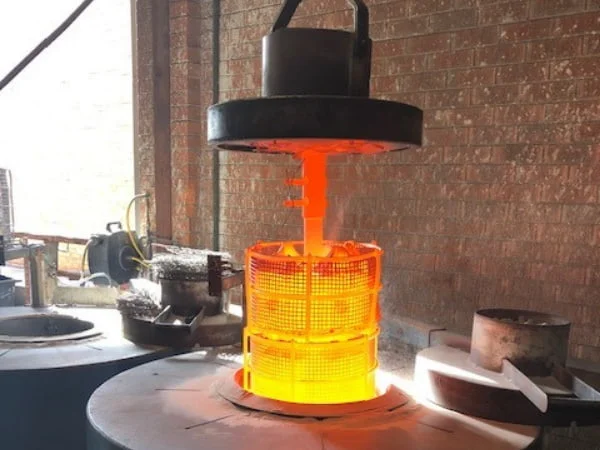
Tempering
Tempering is a refinement process that aims to reduce brittleness in the metal and achieve the desired ratio of hardness to toughness.
Tempering is done by heating the metal to below its critical temperature and allowing it to be air-cooled. The temperature to which the metal is heated determines how much hardness is removed. The chemical composition of the metal also plays a role in its optimal tempering temperature.
Metals that are meant to remain hard are tempered at low temperatures in the range of 66 to 148 °C. This has minimal effect on the hardness of the metal and only serves to relieve some of its internal stresses.
However, metals that need to be ductile or deformable are tempered at much higher temperatures in the range of 300 to 500 °C, to significantly reduce hardness and brittleness.
Buy metal online from Edcon Steel
Edcon Steel is Australia’s most comprehensive online steel and metal superstore, so if you’re looking for products for your next project, we’ve got you covered. We cut and supply steel and metal – in a wide range of shapes, sizes and grades – for all your project needs.
Read more steel articles to find out more about the steel industry, customer projects and product resources.
Buy steel online. Delivery or in-store pick up.

Huge Stock
Levels

Buy Online
24/7

Custom Cut
or Order
