How to choose the right steel coating for the job
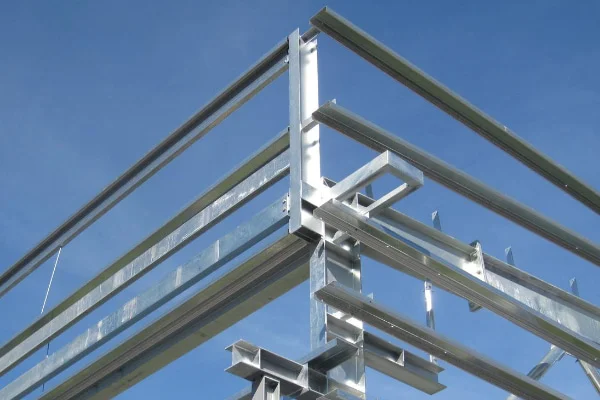
If you want increased durability and corrosion resistance, coated steel is the answer.
But choosing the right steel coating is often where you can come unstuck.
And that’s because there isn’t a simple answer to choose which is the best option for your project.
At Edcon Steel we offer both painting and galvanising for steel fabrication projects.
But which you choose will depend on a range of factors… and there are pros and cons for each.
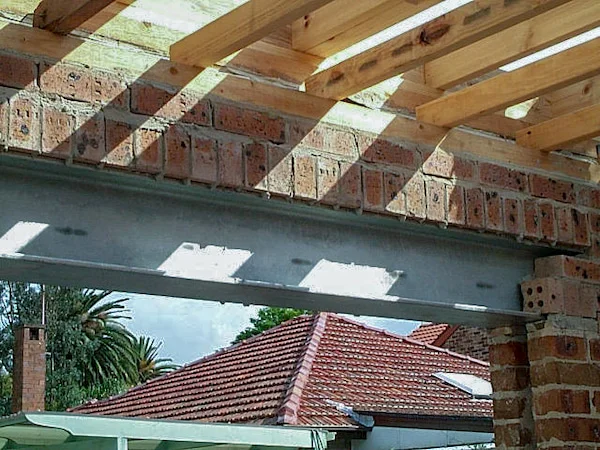
Where to start
Generally speaking, for structural steel that will be located outdoors or exposed to the elements, galvanising offers long-life, low maintenance, cost-effective industrial protection.
However, galvanising is a metallic finish that is not always smooth or blemish free, which can result in a non-uniform and inconsistent coating.
If you need a particular coloured finish or smooth and even finish, then painting is the only way to achieve this.
In fact, painting is the preferable option where:
- appearance is a factor
- high tolerances are required
- frames and large fabrications are required
- the structure includes moving parts, such as threads or hinges.
As simple as it sounds, asking to have your steelwork ‘painted’ will not be enough to get a job that will necessarily meet your requirements. Time and care need to be taken to ensure you are getting the right steel coating for your particular application.
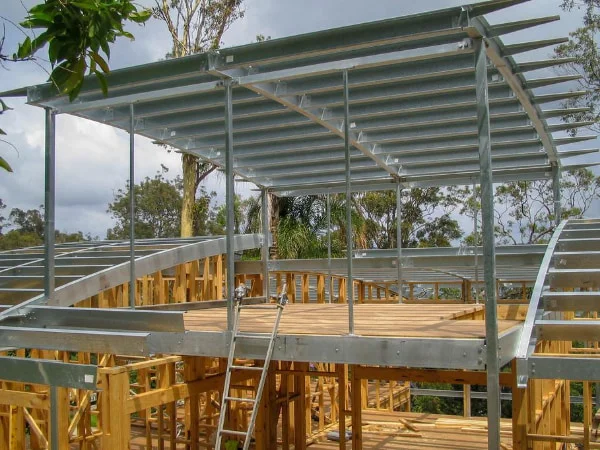
Meeting the Australian Standard for steel coating
Your steel coating shouldn’t be an afterthought. The time to consider which coating option to use is at the start of the job, before you place your order.
And we strongly recommend that you discuss the coating requirements with your designer or refer to the relevant Australian Standard.
Coating of Structural Steel is covered by AS2312:2014 Guide to the protection of structural steel against atmospheric corrosion by the use of protective coatings.
This standard will help you to consider the design life for your project as well as the environment your project is subject to. There are two major categories of coatings and hence the standard has two parts:
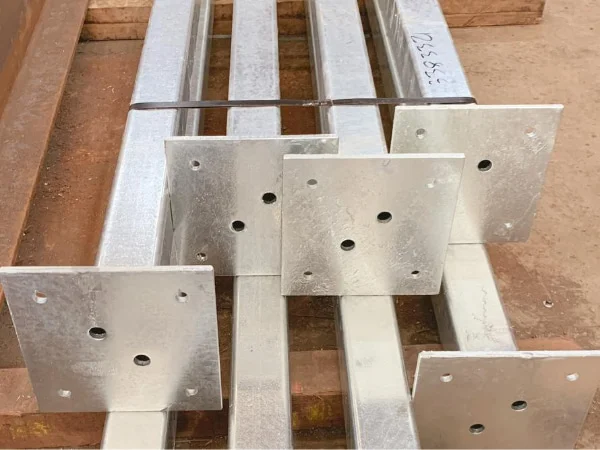
Hot dip galvanising
The process of galvanising steel has been one that has stood the test of time, and for good reason. The chemical bonding of the protective coating (zinc) to the substrate (steel) makes the coating durable, strong and long lasting.
And – unlike painting – galvanising requires no maintenance for up to 10 years in ‘normal’ situations. Painting, on the other hand, requires annual – or more frequent – maintenance regimes to stop the build-up of harmful chemicals on the painted surfaces.
The vast majority of galvanised steel work is done using hot-dip galvanized (zinc) coatings.
However, it’s not as simple as that… hot dip galvanising also has its pitfalls, the first of which is appearance. Some customers love the metallic silver finish but others find it harsh and industrial. Unfortunately for some, there is only one finish available.
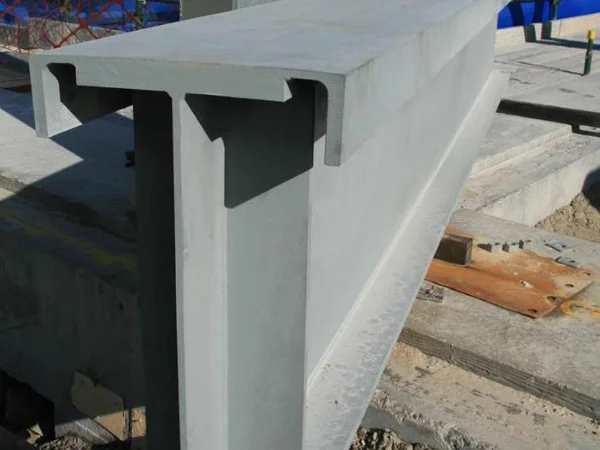
The life of galvanising will also be severely affected by exposure to corrosive chemicals, mechanical damage, running or moving water (especially sea water), electrochemical corrosion through contact with incompatible materials and prolonged contact with certain chemicals.
Distortion can also be a problem with galvanising. The galvanising process heats the steel up to a temperature where the steel has about half of the strength it has at room temperature.
Any residual stress in the steel releases at the high temperature, causing distortion. Edcon Steel Managing Director, Hugh Edmunds, explains:
“We once fabricated a composite crane beam for a major water project. The beam needed to be straight and true, due to its application as a crane runway beam. ”
“The nature of the beam ruled out galvanising as an option. We couldn’t risk possible distortion, so we were able to provide a comparable painting option.”
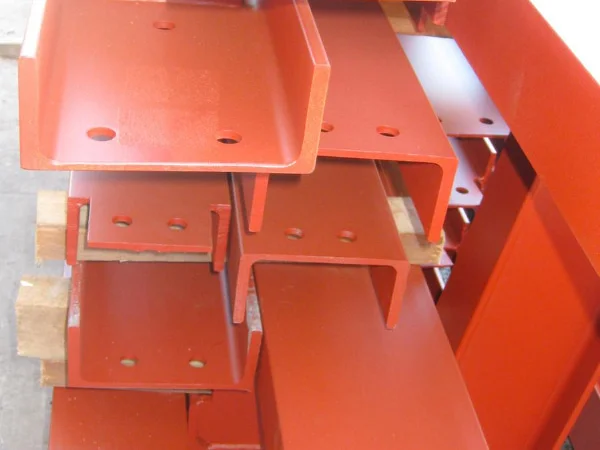
Paint coating
Not all paints are created equal. The performance of your paint system is only as good as the item the paint is applied to. Dirty, oily or rusty steel items can be painted… but they will not last nearly as long clean and properly treated steel. Surface treatment is a huge consideration. And it’s a consideration that can represent up to 50% of the costs of the coating.
Next, you’ll need to look at what paint to use. And it’s a choice you will make based on the environment the steel will be located in and how long you need it to last. For assistance with the selection of a suitable painting system, have a look at the summary from Dulux of AS2312: 2.
Here are some preliminary costs (ex-GST) to help you compare the options (as at 1 July 2023):
- Whip blast and one coat of Red Oxide (ROZC) will be $1,458.00 per tonne* (rates may change subject to volume and surface area per tonne)
- Pickle and hot dip galvanising will be $2,038.00 per tonne* (rates may change subject to sizes, volume and surface area per tonne)
- 2.5 Class 3 coat paint system $4,880 – 12,800 per tonne* (rates will change subject to specifications, volume and surface area per tonne).
*Please note these rates are provided as a guide for customers. These are not a formal offer, Edcon Steel will need to review your project before accepting work at these rates.
Are you ready to choose Edcon as your steel fabricator?
Edcon Steel is Australia’s most comprehensive online steel and metal superstore, so if you’re looking for products for your next project, we’ve got you covered. We cut and supply steel and metal – in a wide range of shapes, sizes and grades – for all your project needs.
Read more steel articles to find out more about the steel industry, customer projects and product resources.
Buy steel online. Delivery or in-store pick up.

Huge Stock
Levels

Buy Online
24/7

Custom Cut
or Order
