The differences between aluminium grades and tempers
Aluminium is one of the most versatile materials. Thanks to its flexibility and adaptability, aluminium is useful in a wide variety of applications. And one of the most common methods of altering the mechanical properties of aluminium is through tempering.
As tempering can have a pronounced effect on aluminum, it’s important to understand what the tempering designations of aluminium are and what each of them mean, to avoid fracturing and potential mistakes.
At Edcon Steel we are proud to provide a range of locally manufactured metal, including aluminium. Our experienced team can help you with sourcing all your aluminium for your projects.
While we don’t stock every grade and temper of aluminium, you will find the grades and tempers clearly identified for each stock item in the range. If you need a grade or temper not listed on our website, please contact us and we will do our best to source it for you.
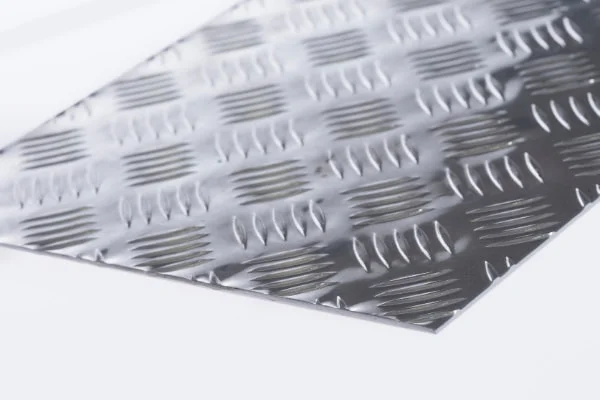
Aluminium tempering designation
Aluminium uses a range of letters and numbers to help you differentiate between its types and understand how to use the material. The best way to understand aluminium is learning aluminium tempering designations.
An aluminium tempering designation is a series of letters and numbers that are used to denote what type of tempering treatment an aluminium alloy has undergone.
Understanding aluminium temper designations is vital to picking the correct material for your next project. That’s because an aluminium alloy can be exactly the same in terms of chemical makeup as another aluminium alloy, but if the two have different tempering designations, the mechanical properties of both alloys could be significantly different.
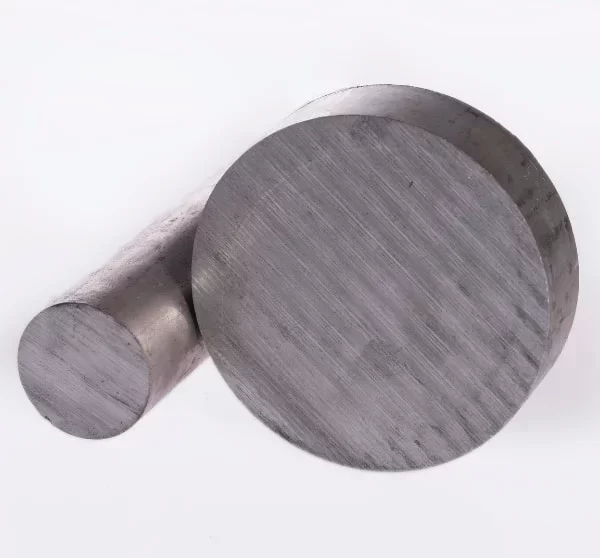
The five letter designations
Within these designations are a few types. There are five main types of aluminium tempering designations. The types are denoted by a letter that precedes a number. The five letter designations are:
- T: Thermally treated. This applies to any product form of any heat-treatable alloy that has been given a solution heat treatment followed by quenching and ageing.
- H: Strain hardened. This is for non-heat-treatable alloys that have had their strength increased by strain hardening, usually at room temperature.
- O: Annealed. Annealing treatments are used to achieve the lowest-strength condition for the alloy. The main reason is to maximise workability or increase toughness and ductility.
- F: As fabricated. Most F-temper products are ‘semi-finished’ products. They will be used in shaping, finishing or thermal processes to achieve other finished forms or tempers.
- W: Solution heat-treated. This designation applies only to alloys that age naturally and spontaneously after solution heat treating. It is rarely a finished temper.
Following the letters of an aluminium temper designation are numbers. The numbers specify exactly how the tempering method was performed.
For instance, a T5 and a T6 are both thermally treated; however, a T5 indicates that the aluminium alloy was cooled from a high-temperature shaping process and artificially aged. Whereas a T6 was solution heat treated and then artificially aged.
The difference in a number in an aluminium temper designation can inform the purchaser of an aluminium alloy about a nuance that could have a significant impact on the mechanical properties of the alloy.
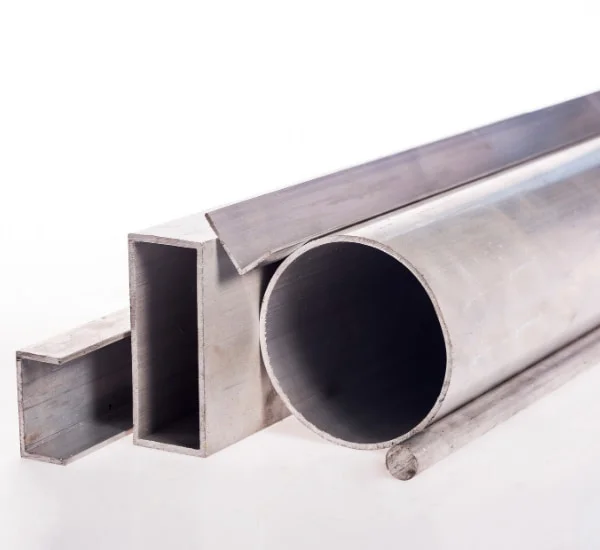
'T' number variations
While there are many variations of numbers that can be used, the ‘T’ number variations are the most commonly used, so it’s important to understand these variations. Here are some of the ‘T’ designation number variants:
- T1: Naturally aged after cooling from an elevated temperature from a forming process
- T2: Cooled from an elevated temperature forming process, cold worked, then naturally aged
- T3: Solution heat treated, cold worked, then naturally aged
- T4: Naturally aged after a solution heat treatment
- T5: Artificially aged after cooling from an elevated temperature from a forming process
- T6: Artificially aged after cooling from a solution heat treatment
- T7: Solution heat treated then over-aged
- T8: Solution heat treated, cold worked, then artificially aged
- T9: Solution heat treated, artificially aged, then cold worked
- T10: Cooled from an elevated temperature forming process, cold worked, then artificially aged.
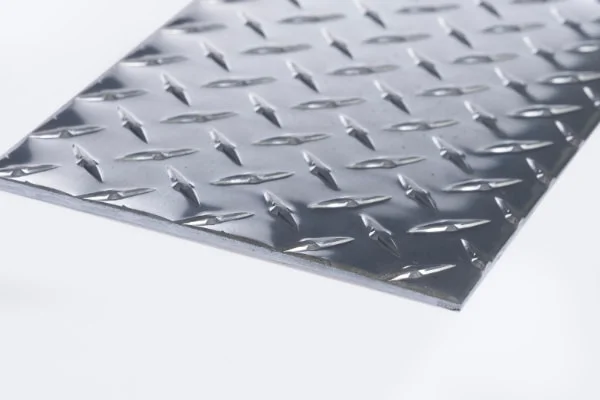
Aluminium grades
While aluminium tempering designation is about letters and numbers that identify types of tempering, aluminium grades are about identifying the aluminium material’s type of usage. Understanding various aluminium grades will help you determine what alloys of aluminium to use in your next project.
We have compiled a short breakdown of each grade’s properties:
Alloy 1100: This grade is commercially pure aluminium. It is soft and ductile and has excellent workability, making it ideal for applications with difficult forming. It can be welded using any method, but it is non heat-treatable. It has an excellent resistance to corrosion and is commonly used in the chemical and food processing industries.
Alloy 2011: High mechanical strength and excellent machining capabilities are the highlights of this grade. It is often called Free Machining Alloy (FMA), an excellent choice for projects done on automatic lathes. The high-speed machining of this grade will produce fine chips that are easily removed. Alloy 2011 is an excellent choice for production of complex and detailed parts.
Alloy 2014: A copper based alloy with very high strength and excellent machining capabilities. This alloy is commonly used in many aerospace structural applications, due to its resistance.
Alloy 2024: One of the most commonly used high strength aluminium alloys. With its combination of high strength and excellent fatigue resistance, it is commonly used where a good strength-to-weight ratio is desired. This grade can be machined to a high finish and it can be formed in the annealed condition with subsequent heat treating, if needed.
Alloy 3003: The most widely used of all aluminium alloys. A commercially pure aluminium with added manganese to increase its strength (20% stronger than the 1100 grade). It has excellent corrosion resistance, and workability. This grade can be deep drawn or spun, welded or brazed.
Alloy 5005: Of all the sheet and plate aluminium forms, Alloy 5005 is the most common. It is a medium strength, general purpose alloy with good weldability.
Alloy 5052: This is the highest strength alloy of the more non heat-treatable grades. Its fatigue strength is higher than most other aluminium grades. Alloy 5052 has a good resistance to marine atmosphere and salt water corrosion, and excellent workability. It can be easily drawn or formed into intricate shapes.
Alloy 5083: This alloy, while not recommended for use in high temperatures above 65°C, does maintain a very high level of strength after welding. It also has excellent ductility so retains good formability. Alloy 5083 is commonly used in marine applications due to its high resistance to corrosion. It is also common in road transport vehicles.
Alloy 6060: This is a medium strength heat treatable alloy and is the most popular extrusion alloy. You will typically find Alloy 6060 used for architectural applications such as complex cross sections or where anodising is required. It offers good corrosion resistance, weldability and cold formability.
Alloy 6061: The most versatile of the heat-treatable aluminium alloys, while keeping most of the good qualities of aluminium. This grade has a great range of mechanical properties and corrosion resistance. It can be fabricated by most of the commonly used techniques and it has good workability in the annealed condition. It is welded by all methods and can be furnace brazed. As a result, it is used in a wide variety of products and applications where appearance and better corrosion resistance with good strength are required.
Alloy 6063: Commonly known as an architectural alloy. It has reasonably high tensile properties, excellent finishing characteristics and a high degree of resistance to corrosion. Most often found in various interior and exterior architectural applications and trim. It is very well suited for anodising applications.
Alloy 7075: This is one of the highest strength aluminium alloys available. It has an excellent strength-to weight ratio, and it is ideally used for highly stressed parts. This grade can be formed in the annealed condition and subsequently heat treated, if needed. It can also be spot or flash welded (arc and gas not recommended).
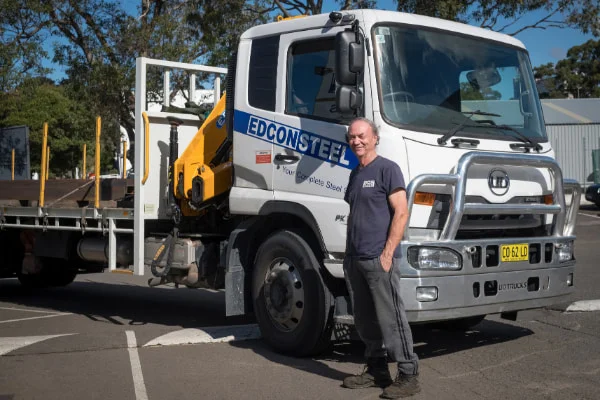
Unique factors for different aluminium grades
Your aluminium grade shouldn’t be an afterthought. The type of aluminium grade you choose will depend on how you intend to use the metal.
Your unique use or project allows you to rank the characteristics of each aluminium grade and will help you narrow down the list of suitable grades.
Regardless of your project or what you intend to use the metal for, think about factors such as machining, corrosion resistance, heat treating, strength or formability to help you narrow your choices and, ultimately, achieve a successful metal project.
All your aluminium requirements under one roof
Edcon Steel is Australia’s most comprehensive online steel and metal superstore, so if you’re looking for products for your next project, we’ve got you covered. We cut and supply steel and metal – in a wide range of shapes, sizes and grades – for all your project needs.
Read more steel articles to find out more about the steel industry, customer projects and product resources.
Buy steel online. Delivery or in-store pick up.

Huge Stock
Levels

Buy Online
24/7

Custom Cut
or Order
